ایران در صدر کشورهای تولیدکننده فولاد خاورمیانه و در رده دهم کشورهای بزرگ تولیدکننده جهان قرار دارد و این در حالی است که صنعت فولاد کشورمان از بهرهوری بالایی برخوردار نیست؛ چراکه کشورهای برتر در این زمینه به مدد تکنولوژی پیشرفته، ماشینآلات و اتوماسیون صنعتی با بهرهوری بسیار بالاتر و قیمت تمامشده کمتر تولید میکنند. سالیانه ۳۰ میلیون تن فولاد در کشور تولید میشود، درحالیکه ما ظرفیت تولید ۴۵ میلیون تنی داریم، قیمت بالای سنگآهن و مواد اولیه وارداتی، محدودیتهای انرژی (برق و گاز)، بیثباتی مقررات و صدور بخشنامههای خلقالساعه، مداخله قیمتی دولت در بازار فولاد، مسئله آب و شکلگیری جریانی از رشد تولید فولاد در خاورمیانه که میتواند تهدیدی برای صادرات فولاد ایران در سالهای آینده باشد، از جمله چالشهای حوزه تولید و تجارت فولاد کشور است.
دکتر ماشاالله سهراب نژاد، مدیرعامل شرکت فولاد زرند ایرانیان یادآوری میکند که نیازهای زیرساخت فولاد اگر بهدرستی مدیریت شود، در استان کرمان فراهم است. اگرچه آب مسئله ی مهمی است، اما فولاد زرند ایرانیان با توجه به این که آب مصرفی خود را از طریق پساب فاضلاب شهری تأمین میکند، از این بابت با چالش جدی روبه رو نیست و با اتمام پروژه فاضلاب زرند نیز این مهم بهطورکلی در زیسکو به یک نقطه قوت تبدیل میشود.
وی همچنین میگوید که توسعه و رونق صنعت فولاد ایران با توجه به تحریمها و مسائل ارزی، تنها از مسیر بومیسازی اتفاق خواهد افتاد. باید به سمت مدیریت بهینه منابع و افزایش بهرهوری، تولید فولادهای خاص و توسعه اکتشاف منابع معدنی در راستای تأمین نیاز فولادسازان گام برداشت.
جذابیت تولید فولاد در ایران را چه عواملی توضیح میدهد؟ و چگونه کشورمان به یک تولیدکننده برتر فولاد در دنیا تبدیل شده است؟
استفاده از صنعت فولاد در تولید، یکی از عوامل تأثیرگذار در صنعت و اقتصاد کشور به شمار میآید. این عامل موجب سازندگی، توسعهیافتگی و پیشرفت کشور و جوامع مختلف شده است.
با نگاهی دقیقتر به زندگی روزمره خود، متوجه حضور صنعت فولاد میشوید که هر روز با آن سروکار دارید. بخش زیادی از تجهیزات و قطعات مورداستفاده روزانه ما از فولاد تولید شدهاند.
صنعت فولاد از همان مراحل آغازین استخراج سنگ آهن از معدن تا هنگام تولید و در زمان مصرف در صنایع پاییندستی، منجر به اشتغالزایی و تولید مشاغل متعدد میشود. برای روشن شدن موضوع کافی است توجه داشته باشیم که به ازا هر نفر شاغل در بخش فولاد در حدود 15 تا 20 نفر بهطور غیرمستقیم فعال خواهند بود.
صنعت فولاد در هر کشور بهعنوان صنعت مادر شناخته میشود و همین موضوع موجب شده است تا پایه و اساس تمامی فعالیتهای اقتصادی بوده و موجب رشد و توسعه شود. هنوز میزان مصرف سرانه فولاد در کشورها نشانه رشد یافتگی و شاخص توسعه تلقی میشود.
تبدیل کشورمان به یکی از تولیدکنندگان مطرح فولاد، مرهون وجود منابع و معادن غنی و نیروی انسانی توانا است که البته راه درازی در جهت کسب جایگاهی که حق خودمان می دانیم پیش رو داریم و قطعاً بهتر خواهیم شد، اگر با برنامهریزی یکپارچه، دستیابی به منابع زیرزمینی را بهتر مدیریت کنیم و در جهت ماندگاری در بازار جهانی، مقوله کیفیت را مدنظر داشته باشیم.
بهرهوری در صنعت فولاد کشورمان و دیگر کشورهای برتر در این صنعت را چگونه مقایسه میکنید؟
بهرهوری مهمترین عامل رقابت در هر صنعتی است. خوشبختانه ایران منابع طبیعی موردنیاز این صنعت ازجمله معادن کانیهای فلزی، غیرفلزی و منابع انرژی مانند گاز و زغالسنگ را بهوفور دارا است. ایران در بین ۱۰ تولیدکننده برتر دنیا جای دارد و همچنین دارنده رتبه اول در بین تولیدکنندگان آهن اسفنجی جهان بر پایه گاز است، اما داشتن منابع و حجم بالای تولید الزاماً نشاندهنده بهرهوری در همه عوامل در این صنعت نیست. بهرهوری بالا در مدیریت بهینه مواد، منابع و مصرف انرژی در راستای کاهش قیمت تمام شده است. متأسفانه صنعت فولاد در ایران در مقایسه با سایر کشورها از بهرهوری بالایی برخوردار نیست، چون در دیگر کشورهای برتر در این زمینه به علت وجود تکنولوژیهای پیشرفته، ماشینآلات مدرن و اتوماسیون صنعتی، بهای تمام شده کمتر میشود؛ بهطور مثال در کره جنوبی و ژاپن بهطور متوسط در حدود ۳0۰۰ تن و در ایران ۵۵۰ تن به ازای هر کارگر، تولید میشود که به این معنی است که بهرهوری نیروی انسانی در کشورهای یاد شده، ۶ برابر ایران است.
از طرف دیگر با وقوع انقلاب صنعتی چهارم که شدیداً بر سرعت تغییرات فناوری اثر داشته، کشورهای برتر صنعت فولاد، تغییرات خود را در این زمینه آغاز نموده اند که این مهم نیز منجر به کاهش هزینهها و افزایش سودآوری و به عبارتی بهرهوری بالاتر میشود. حال بایستی با سرمایهگذاری و ایجاد زیرساختهای تحقیق و توسعه، پیادهسازی تکنولوژیهای مدرن و مدیریت بهینه مصرف منابع بویژه منابع انرژی و همچنین مدیریت صحیح سرمایه انسانی و افزایش خلاقیت و همچنین گام نهادن در مسیر انقلاب صنعتی چهارم، بهرهوری را افزایش دهیم. ایران در صدر کشورهای تولیدکننده فولاد در خاورمیانه و در رده ۱۰ کشور بزرگ تولیدکننده فولاد در جهان قرار دارد. بااینحال، برای بهرهبرداری کامل از پتانسیل تولید فولاد نیازمند بهبود فرآیندهای تولید، بهبود کیفیت و بازاریابی صادراتی محصولات فولادی و سرمایهگذاری بیشتر در این صنعت است.
در مورد چگونگی کیفیت و رتبه در شاخص رقابتپذیری صنعتی فولاد تولید ایران بهطورکلی و تولیدات شرکت فولاد زرند ایرانیان بهطور مشخص چه توضیحاتی ارائه مینمایید؟
شاخص رقابتپذیری صنعتی فولاد معیاری است که برای اندازهگیری و مقایسه عملکرد صنعت فولاد ایران با کشورهای دیگر به کار میرود. این شاخص بر اساس متغیرهای مختلفی مانند ظرفیت تولید، کیفیت محصولات، هزینههای تولید، توسعه صادرات، محیطزیست و ایمنی، توانایی رقابت با بازارهای جهانی، بهرهمندی از تکنولوژی بهروز، معادن سنگآهن و زغالسنگ و ریسکهای کشوری و غیره محاسبه میشود.
بر اساس آمار منتشر شده توسط انجمن جهانی فولاد، در حال حاضر ایران در رتبه دهم تولیدکنندگان فولاد جهان قرار دارد و لازمه رقابتپذیری فولاد ایران، توسعه معادن سنگآهن و زغالسنگ، بهبود زیرساختهای حملونقل و پرهیز از صدور بخشنامههای خلقالساعه و محدودیتهای ارزی و از همه مهمتر رفع محدودیتهای برق و گاز است.
شرکت فولاد زرند ایرانیان با توجه به دارا بودن زنجیره کامل تولید از معادن سنگآهن و زغال تا تولید شمش فولاد دارای مزیت رقابتی ویژهای در این خصوص است. لازم به ذکر است که شرکت فولاد زرند ایرانیان با درک اهمیت این موضوع که میزان مصرف فولاد در کشور بهمراتب کمتر از ظرفیتسازیهای انجام شده در این صنعت است، اهتمام ویژهای به افزایش بهرهوری، کاهش قیمت تمام شده، برندینگ و بازارسازی محصولات دارد و بخصوص با توجه به روش تولید فولاد در این شرکت که بر مبنای استفاده از کوره بلند است، از مزیت نسبی در کیفیت برخوردار است و محصولات این شرکت مطلوبیت لازم را دارد.
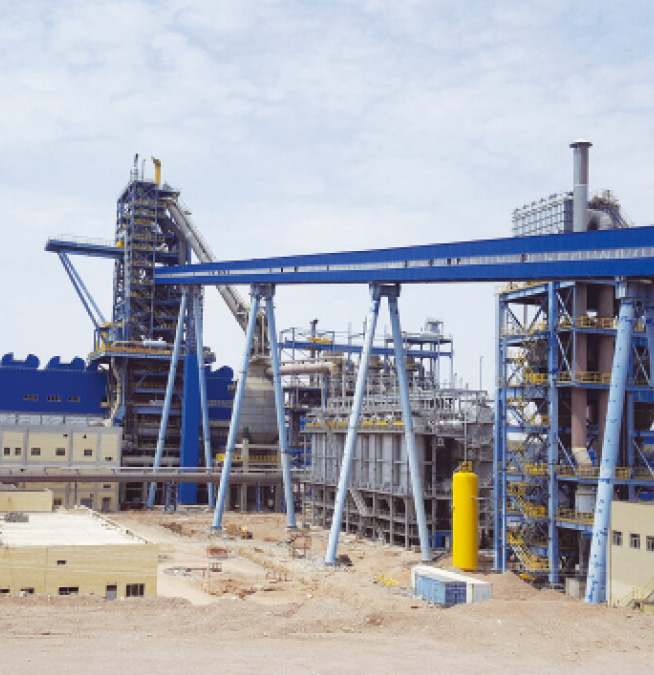
بومیسازی چند درصد قطعات، تجهیزات و مواد مصرفی در فولاد یا تولیدات شرکت فولاد زرند ایرانیان وجود دارد و این بومیسازی چه تأثیری در اندازه هزینههای تولید داشته است؟
فولاد زرند ایرانیان بهعنوان یکی از بزرگترین زنجیرههای تولیدی فولاد کشور از معدن تا شمش همواره نگاهی همافزا به پتانسیلهای استان داشته است.
فارغ از شعار، این مهم است که در عمل شرکتهای بزرگ دست شرکتهای کوچکتر را بگیرند و به آنها کمک کنند.
وجود چند شرکت بزرگ در استان دلیل بر صنعتی شدن استان نیست؛ صنعتی شدن یک منطقه زمانی اتفاق میافتد که صنعت در ابعاد مختلف آن به نواحی و حاشیه شهرها در قالب شهرکها و واحدهای صنعتی مرکب از کارگاههای کوچک رسوخ پیدا کند و حس صنعتی شدن فراگیر گردد و اشتغال در واحدهای صنعتی پراکنده نقش قابلتوجهی پیدا کند و مردم در ابعاد وسیع درگیر صنعت شوند.
فولاد زرند ایرانیان تقویت اقتصاد استان را همواره در صدر برنامههای خود قرار داده و اکنون با اطمینان اعلام مینمایم که بیش از 70 درصد خریدهای داخلی ما از داخل استان صورت میگیرد. استراتژی ما این است که مواد اولیه، قطعات، وسایل و کلیه نیازهای شرکت را از تأمینکنندگان بومی تهیه کنیم و در همین راستا، کمیته بومیسازی بازرگانی جهت انتقال درخواست خریدهای خارج به سمت خرید داخل کشور و استان تشکیل گردیده است که این کمیته موفق گردید در سال مالی گذشته 45 درصد از درخواستهای تأمین از خارج را بهسوی تأمین از داخل و یا جهت بررسی فنی بیشتر مطابق با امکانات ساخت داخل کشور و یا استان سوق دهد که این امر مهم منجر به حفظ منابع ارزی شرکت گردید.
مصرف حداکثری از ظرفیت تولید فولاد در کشور چقدر است؟
خوشبختانه یا متأسفانه سالیانه ۳۰ میلیون تن فولاد در کشور تولید میشود. خوشبختانه از این جهت که ایران در زمینه تولید فولاد جزو ۱۰ کشور اول دنیا است، اما متأسفانه از این نظر که ما ظرفیت تولیدی معادل ۴۵ میلیون تن در سال را داریم که به دلایل متعدد نمیتوانیم از آن بهرهبرداری کنیم؛ درحالیکه اگر حتی ۹۰ درصد این ظرفیت را محقق کنیم شاید به رتبه پنجمین یا ششمین تولیدکننده دنیا دست یابیم.
این صنعت در صادرات و ارزآوری با چه موانعی مواجه است؟
با جنگ روسیه و اوکراین، نوسانات قیمت شمش باعث شد که بسیاری از تولیدکنندگان دنیا از چرخه فعالیت خارج شوند. همچنین عواملی مانند عوارض گمرکی، بالا بودن هزینه حمل تا بندرعباس، هزینههای انبارداری و برخی موارد دیگر از موانع رو به روی صادرات است.
در کل چالشهای تجارت بینالمللی زنجیره صنعت فولاد و راهحلها چیست؟
یکی از چالشهایی که صنعت تولید فولاد با آن مواجه است، قیمت سنگآهن و مواد اولیه وارداتی است و فولاد زرند ایرانیان که نیاز به واردات قطعی زغال سنگ کنسانتره مرغوب از خارج از کشور دارد بیش از سایر تولیدکنندگان فولاد، با این چالش مواجه است؛ زیرا با بالا رفتن نرخ دلار، قیمت مواد اولیه وارداتی و هزینههای تولید بالا رفته و بازار دچار گرانی میشود. مهمترین چالش صنعت فولاد کشور در سال جاری و البته برای کل صنعت کشور بحث محدودیتهای انرژی است که میتواند بلندپروازی این صنعت برای حضور در بخش بینالمللی را متوقف کند.
در تجارت بینالملل، مهمترین تبعات جنگ روسیه و اوکراین چرخش تمامعیار روسیه به سمت شرق به دلیل تحریمهای غرب است. روسیه برای پر کردن خلأ ناشی از کمبود درآمدهای خود از غرب به سمت شرق حرکت و اقدام به دامپینگ در بازار کرد و به همین دلیل کشورهای دیگر ناچار شدند که تخفیفهای گستردهای را برای محصولات خود ارائه دهند. انجمن فولاد ایران میگوید که این تغییر رویه برای فولادسازان ایرانی به معنای ظهور رقیبی جدید و احتمال تصاحب بازارهایی است که فولاد ایران در اختیار دارد. بااینحال مقاصد صادراتی ایران تنها از سوی روسیه تهدید نمیشود. پاکستان در جنوب شرق ایران در حال توسعه طرحهای فولادی است. در جنوب هم امارات متحده عربی موفق شده با تأمین گاز موردنیاز، طرحهای فولادی تعریف کند. عمان و عربستان هم که طرحهای جدید فولادی در دستور کار دارند؛ همه اینها به معنای شکلگیری جریانی از رشد تولید فولاد در منطقه خاورمیانه است که میتواند تهدیدی برای صادرات فولاد ایران در سالهای پیش رو به شمار آید.
موانع بازرگانی بویژه بازرگانی خارجی و صادرات فولاد، زمانی میتواند کاهش یابد که دولت و مجلس، سیاستهای متعادل و باثباتی را پیش بگیرند، ولی اگر این ثبات ایجاد نشود، تولیدکننده جهت خرید ارز موردنیاز خود برای تهیه مواد اولیه وارداتی و نیز در بازگرداندن ارز حاصل از صادرات خود، دچار مشکل میشود و نمیداند چه اتفاقی رخ میدهد. به هر صورتمسئله عدم ثبات بهعنوان یک مانع صادراتی، دست مدیران را میبندد و به نظر من خیلی بیشتر از تحریمهای خارجی اثر منفی دارد.
مهمترین چالش صنعت فولاد کشور در سال جاری و البته برای کل صنعت کشور، بحث محدودیتهای انرژی است که میتواند بلندپروازی این صنعت برای حضور در بخش بینالمللی را متوقف کند. تأمین انرژی برای تولیدکنندگان فعال در زنجیره فولاد ایران یک چالش است و نبود گاز و برق موردنیاز تولید در فصول اوج مصرف، یک بحران به شمار میآید. در پی وقوع این بحران که فولادسازان ایرانی دو بار در سال آن را تجربه میکنند، فعالیت واحدهای فولادی یا متوقف میشود و یا به کمترین میزان کاهش پیدا میکند. بر اساس گزارش انجمن فولاد ایران، در ماههای گرم تیر و مرداد با اوجگیری مصرف برق و در ماههای سرد دی و بهمن با شدت گرفتن مصرف گاز، بیشتر ذخایر این دو منبع انرژی به تأمین نیاز خانوار اختصاص پیدا میکند و بسیاری از صنایع از جمله صنعت فولاد از تولید بازمیمانند.
ارزیابی شما از مکانیزم بهکارگیری دولت برای تنظیم بازار فولاد چیست؟ چه پیشنهاداتی را برای بهینهسازی وضع بازار ارائه مینمایید؟
یکی از چالشهای مهم زنجیره فولاد، تنظیم بازار فولاد کشور است. با توجه به شرایط تحریم و نوسانات نرخ ارز در سالهای اخیر، دولت مداخلات گستردهای برای تنظیم بازار فولاد کشور انجام داده است. مداخله دولت برای تنظیم بازار فولاد بهطور عمده از طریق ستاد تنظیم بازار و صدور بخشنامهها و دستورالعملهای مختلف بوده که مجموعه سیاستهای تنظیم بازار دولت، منفعتی به مصرفکنندگان نهایی کالاها (مردم) نرسانده است، درعینحال قیمت تمام شده محصولات فولادی غالباً بیشتر از قیمت فروشهای دستوری است که این مسئله تبعات جدی به دنبال خواهد داشت و بنگاههای اقتصادی در حوزه فولاد را با مشکل مواجه مینماید.
همیشه عرضه و تقاضا قیمتها را بهدرستی تنظیم میکند و اگر اقتصاد آزاد در کشور جاری باشد هر کالایی در نقطه درست قیمت خود خواهد ایستاد و هم تولیدکننده و هم مصرفکننده در تعیین این قیمت نقش خواهند داشت.
سیاستهای مداخله قیمتی دولت در بازار محصولات زنجیره فولاد موجب شده تا شکاف قیمتی قابل-توجهی میان قیمتهای داخلی و جهانی ایجاد شود که این مسئله به همراه کاهش ارزش ریال باعث شده تا جذابیت صادرات افزایش یابد. رشد صادرات محصولات مختلف زنجیره فولاد به همراه کاهش عرضه داخلی، دولت را به سمت کنترل صادرات و وضع عوارض صادراتی برای مواد معدنی و فلزی سوق داد. بهطوریکه اقداماتی که ذکر خواهد شد که عمدتاً برخلاف قوانین و مقررات جاری کشور هستند و با مصوبه ستاد تنظیم بازار قابلیت اجرا پیدا کردهاند، برای کنترل قیمتها و حفظ توازن زنجیره انجام شده است:
1. قیمتگذاری محصولات مختلف زنجیره ارزش فولاد، آن هم بدون رعایت تناسب لازم بین هزینههای مربوطه،
2. الزام تولیدکنندگان عمدتاً بزرگ به عرضه ماهیانه شمش و محصولات فولادی در بورس کالا به میزان مشخص،
3. ایجاد محدودیتهای مختلف برای صادرات واحدهایی که سهم تعیین شده توسط دولت را در بورس کالا عرضه نکردهاند (اجرای این بند در بازههای زمانی مختلف از سال ۱۳۹۷ تاکنون به صورت مستمر و منظم نبوده است)،
4. ابطال معاملات بورس کالا،
5. ممنوعیت صادرات توسط بازرگانان و محدود کردن صادرات صرفاً به تولیدکنندگان،
6. وضع عوارض صادراتی 20 درصدی برای سنگآهن، کنسانتره و گندله و از همه مهمتر بعضاً افزایشهای نجومی و از همه بدتر عطف به ماسبق شدن و تحمیل بار مالی غیرقابلتحمل به تولیدکنندگان،
7. تعدد بخشنامهها و دستورالعملهای صادره از سوی ستاد تنظیم بازار، موجب ایجاد بروکراسی و ابهامات متعدد در تنظیم بازار زنجیره فولاد شده و تصمیمات خلقالساعه و غیرکارشناسی، آینده این صنعت را با مخاطراتی روبه رو کرده است. بررسی آمار و اطلاعات ارائه شده از سوی شرکت بورس کالا و گمرک جمهوری اسلامی ایران نشان میدهد که بخشنامهها و دستورالعملهای صادره موجب عرضه کالا در بازار داخلی و تأمین پایدار نیاز زنجیره نشده است.
بهعلاوه یک کارخانه بخش خصوصی که مطابق قانون تجارت و با سرمایهگذاری غیردولتی و بهصورت انتفاعی مواد اولیه خود (زغال و کک، قراضه، آهن اسفنجی و فروآلیاژها) را از بازار آزاد و نزدیک به قیمتهای جهانی تأمین و با حاشیه سود کمتر از ۱۰ درصد فعالیت مینماید، بر چه اساسی میبایست با دستور دولت محصول تولیدی خود را حدود ۲۰ تا ۳۵ درصد ارزانتر از نرخهای جهانی بفروشد؟ این کار طبیعتاً خلاف عقل اقتصادی سرمایهگذاران بخش خصوصی است و در صورت اجبار، مشکلات تولید بیشتر خواهد شد.
الزام به عرضه کل شمش داخلی در بورس کالا آن هم با مقررات سختگیرانه آن شامل: ضمانتنامههای بسیار سنگین، کارمزدهای زیاد، الزامات پیچیده و متعدد پیش از عرضه، اعمال سلیقهای آییننامهها و از همه مهمتر ابطال معاملات به دلایل عجیبوغریب، بههیچعنوان اجرایی نمیباشد. لذا لازم است شرایط پذیرش، عرضه و معامله در بورس کالا بهمراتب تسهیل شود.
چه ارزیابی از زیرساخت حوزه فولاد در استان کرمان دارید؟
به نظر میرسد اغلب نیازهای زیرساخت فولاد اگر بهدرستی مدیریت شود در استان کرمان فراهم است؛ البته مشکل آب در کل مملکت یک مشکل اساسی است و بخصوص با توزیع کارخانجات فولادی در مناطق کم آب، خود را بیشتر نشان میدهد.
یادآور میشوم که فولاد زرند ایرانیان با توجه به اینکه آب مصرفی خود را از طریق پساب فاضلابهای شهری تأمین میکند از این بابت با چالش جدی مواجه نمیباشد و با اتمام پروژه فاضلاب زرند نیز این مهم بهطورکلی در زیسکو به یک نقطه قوت تبدیل میگردد. منتهی استقرار سایر واحدهای تولید فولاد در کرمان باید با ملاحظه بیشتری انجام میشد که اتکا به منابع آبی روبهزوال، قطعاً در آینده یک معضل جدی خواهد بود.
از طرفی معادن سنگآهن در استان کرمان، تنها پاسخگوی بخشی از تولید فولاد میباشد که باید در آینده نزدیک ساماندهی شود و اکتشافات مرتبط توسعه یابد تا تبدیل به معضلی در آینده نشود. به نظر میرسد کمبود مواد اولیه آهندار بهزودی خود را بیشتر نشان دهد.
در حوزه زغال، کار چندانی در کرمان انجام نشده است و تا آنجا که اطلاع دارم، عمده اکتشافات مربوط به بیش از 50 سال قبل است که توسط روسها انجام شده و متأسفانه تلاشی برای اکتشاف و استخراج زغال کیفی به عمل نیامده و نهتنها از نظر کیفی مشکل دارد و به تعبیری زغال کک شو محسوب نمیشود، بلکه از نظر کمی نیز پاسخگوی نیازهای حداقلی کوره بلند نمیباشد. به عبارتی هم از نظر کیفیت و هم از نظر کمیت در حال حاضر به زغال مرغوب خارجی نیاز شدید میباشد.
از جهت حملونقل و جاده و خطوط ریلی نیز کرمان قابلیتهای قابلتوجهی دارد، منتهی گرانی حملونقل و افزایش شدید قیمتهای مربوطه در یکی دو سال گذشته از رشد قیمت فولاد پیشی گرفته و تأثیر قابلتوجهی در افزایش بهای تمام شده محصولات فولادی دارد.
تابآوری پایدار صنعت فولاد کشور در گرو چه الزاماتی است و چشمانداز رونق و توسعه فولاد کشور را چگونه توضیح میدهید؟
با توجه به نوسانات بازارهای بینالمللی، تغییرات قیمت مواد اولیه، افزایش قیمت حاملهای انرژی، تغییرات سریع فناوری، صنایع فولادی باید برای افزایش تابآوری در این شرایط، عوامل تأثیرگذار را شناسایی کرده و استراتژیهایی جهت افزایش تابآوری در برابر هر کدام از عوامل داشته باشند، از جمله: پیشبینی دقیق قیمت و تقاضا و درنتیجه انعطافپذیری تغییر سرعت تولید، زمان تحویل محصولات و غیره. از دیگر راههای افزایش تابآوری، تنوع در تولید محصولات است و یکی دیگر از عوامل مهم که بسیار بر تابآوری صنایع فولادی با توجه به قطعی گاز در زمستان و برق در تابستان تأثیر میگذارد، مدیریت بهینه و صحیح منابع تولید و انرژی است که برنامهریزی مدون و استراتژیهای مقابله با این مسئله بسیار بر تابآوری و حفظ حاشیه سود صنایع فولادی اثرگذار است. از دیگر عوامل مهم در تابآوری صنایع فولادی، افزایش تابآوری زنجیره تأمین و همچنین طراحی زنجیره تأمین بهینه است که بتواند در برابر تمامی اختلالاتی که ممکن است در تأمین به وجود آید رویکرد مناسبی اتخاذ کند.
توسعه و رونق صنعت فولاد ایران با توجه به تحریمها و مسائل ارزی، تنها از مسیر بومیسازی اتفاق خواهد افتاد و برای رشد و توسعه بیشتر بایستی به سمت افزایش بهرهوری با مدیریت بهتر منابع، تولید فولادهای خاص و همچنین توسعه اکتشاف منابع معدنی در راستای تأمین نیاز فولادسازان گام برداشت.
در پایان چه نکاتی را لازم میدانید که اضافه فرمایید؟
نکاتی که لازم بود توضیح داده شد، منتهی برنامهریزی تولید فولاد با نگرش به زیرساختها و نیازها و معادن و آب و برق و غیره باید از یک پارچگی و تفکر جمعی برخوردار شود. اگر به جغرافیای توزیع کارخانجات که نشأتگرفته از مجوزهای ریزودرشت سالهای اخیر میباشد بهدرستی توجه شود، مشخص میشود که تصمیمات اتخاذشده در سنوات اخیر بیشتر تابع فشارهای بخشی و ناحیهای بوده و از یک برنامه منسجم و آگاهانه تبعیت نکرده است؛ بهعنوانمثال فولاد زرند که سالهاست در استان کرمان فعالیت دارد، اخیراً مجبور شده بخش قابلتوجهی از نیاز سنگآهن خود را از اقصا نقاط کشور از جمله سنگان، سقز و غیره تأمین نماید که هزینه حمل گاهی با هزینه خرید سنگ برابری میکند، درحالیکه بعد از تأسیس این شرکت بسیاری از منابع و معادن در دسترس به واحدهای کوچکی که در گوشه و کنار استان شکل گرفتهاند، اختصاص داده شده و عرصه را بر شرکتهای بزرگتر تنگ نموده است.
در پایان و در یک کلام به مقوله تولید و بخصوص تولید فولاد که عهدهدار اشتغال تعداد کثیری از نیروی انسانی است، باید با نگاهی متمرکزتر توجه شود.