کارشناس ارشد بازارهای بینالمللی معدن و صنایع معدنی
تولید فولاد سبز در کشور و اما و اگرها
تولید فولاد در کشور در کل زنجیره با وجود تمامی کاستیها بهویژه موضوع کمبود انرژی با وضعیت نسبتاً مناسبی روبهرو است. به گفته فولادسازان کشور، در تکنولوژی تولید فولاد هنوز برنامهریزی وسیعی برای تولید فولاد سبز اتفاق نیفتاده است. مالیات کربن برای فولادسازان از سال 2025 بهتدریج و در اوج آن از سال 2030 به بعد، در دنیا وضع خواهد شد؛ به عبارتی هر محصولی که سبز نباشد یا درصد سبز بودن آن کم باشد، مشمول مالیات کربن خواهد شد. منظور از تولید فولاد سبز یعنی کلیه مراحل زنجیره تولید فولاد از جمله استخراج، فرآوری سنگآهن، حمل بهوسیله واگن و یا کامیون تا تولید فولاد در انتهای زنجیره باید سبز و بدون سوخت فسیلی باشد که در این مورد، مسیر بسیار طولانی در پیش روی کشور ما است.
بسیاری از کشورهای مترقی جهان در فولاد بهویژه فولادساز اول جهان یعنی کشور چین، سال 2050 را مبدأ تولید فولاد سبز اعلام نموده بود، اما با شیوع کرونا، تمامی پروژه ها به تعویق افتاد و سال مبنا به 2060 تغییر یافت.
کشور هند سال 2060 را بهعنوان مبدأ تولید فولاد سبز تعیین نموده بود که در بحران همهگیری کرونا بسیار تحت تأثیر قرار گرفت؛ بهطوریکه حتی فولادسازان این کشور که اکثر آنها دارای خطوط تولیدی کوره بلند بودند، تمامی اکسیژن تولیدی را به بیمارستان ها اختصاص دادند و در این دوره هندوستان به علت کمبود انرژی بیشازپیش به استفاده از زغالسنگ روی آورد و طبیعی است که فرآیند سبز شدن فولاد در آنجا 10 سال به تعویق افتاد و به سال 2070 منتقل شد.
به اعتقاد بنده صحبت در مورد فولاد سبز در کشور ما با وجود عقب بودن ما در تکنولوژیهای مربوط به آن، بسیار زود است و باید به مسائل بسیار مهمتر و محدودیتهای فعلی بپردازیم؛ برای مثال با وجود کمبود انرژی، کمبود برق در تابستان و گاز در زمستان، تولید قطعی فولاد در کشور حدود 32 میلیون تن است، درصورتیکه با توجه به ظرفیتهای موجود، امکان تولید تا 40 میلیون تن وجود داشته و دارد.
با توجه به طرح جامع فولاد، ظرفیتهای اختصاص یافته در افق 1404 یا 2025 بالغ بر 55 میلیون تن است که به روایتی تا 70 میلیون تن ظرفیت واگذار شده است. موضوعی که در رابطه با سیر تحول و توسعه صنعت فولاد حائز اهمیت میباشد، این است که این میزان فولاد تولیدی باید در چه مسیری استفاده شود؟ طبیعتاً در داخل کشور پروژههای ساختوساز محدود شده و مازاد بر نیاز داخلی است؛ لذا صادرات مازاد فولاد و کلیه محصولات چرخه زنجیره فولاد از اهمیت بسزایی برخوردار است.
اینکه گفته شود که تحریمها در موضوع صادرات فولاد تأثیرگذار نبوده، درست نیست؛ تحریمهای خارجی مؤثر بوده است، اما واقعیتی که وجود دارد این است که در وضع عوارض صادراتی، محدودیتها و یا تحریمهای داخلی، پروسه صادرات محصولات چرخه زنجیره فولاد را بیشتر از همه تحت تأثیر قرار داده که در دو سال اخیر شدت بیشتری هم پیدا کرده است. در بسیاری از کشورها عوارض صادراتی را بهصورت کنترل شده و محدود وضع میکنند، بهطوری که صدمه جدی به چرخه زنجیره فولاد وارد نشود.
تجربه هندوستان در وضع عوارض صادراتی
این موضوع را بارها و بارها در جراید مختلف مطرح کرده و اینجا نیز مجدد تکرار میکنم که تا سال 2010، هندوستان با صادرات 110 میلیون تن در سال، جزو سه کشور اول صادرکننده سنگآهن به چین بعد از استرالیا و برزیل بود. در سال 2010 با وضع عوارض 30 درصدی صادراتی، شوک شدیدی به بازار وارد و باعث شد که صادرات در این کشور به 15 میلیون تن کاهش پیدا کند. در ادامه این عوارض به 40 درصد افزایش پیدا کرد و در نتیجه صادرات سنگآهن در هندوستان ظرف یکی دو سال به 5 میلیون تن رسید و این امر منجر به کاهش جدی اکتشاف و استخراج در تولید سنگآهن و فرآوری آن گردید و زیان شدیدی به زنجیره فولاد در این کشور وارد نمود؛ بهطوریکه هندوستان مجبور شد که از سال 2015 این قانون را اصلاح کند و عوارض صادراتی 30 درصدی را فقط برای عیار 58 درصد به بالا وضع و صادرات عیار آهن 58 درصد و پایینتر از آن را آزاد کند. این حرکت موجب شد که فعالیت معدنکاری در هندوستان مجدد توسعه پیدا کند. هندوستان در سال 2017 بعد از اطمینان از تأمین خوراک سنگآهن فولادسازان در کشور، اعلام کرد که در افق 2030، به تولید 300 میلیون تن فولاد خواهد رسید، با این روند بهبود تولید فعالیت معدنکاری هندوستان حتی در زمان کرونا توسعه پیدا کرد؛ بهطوریکه هندوستان سال 2022 اعلام نمود که نهتنها در افق 2030 به تولید 300 میلیون فولاد میرسد بلکه طبق برنامهریزی در افق 2047 به تولید 500 میلیون تن فولاد خواهد رسید.
تجربه هندوستان نشان میدهد که اگر عوارض صادراتی کنترل نشود، ضرر وحشتناکی به کشور وارد میشود. عقبگرد بهموقع هندوستان هرچند که با تأخیر چندساله همراه بود، باعث حمایتهای لازم شد و حتی این حرکت، عوارض صادراتی زیر عیار 58 درصد را صفر کرد؛ چون هندوستان معتقد بود که سنگآهن پرعیار که نیاز داخل کشور است، نباید صادر شود.
در رابطه با ایران مسئله متفاوت است، به علت محدودیتهای برق در تابستان و گاز در زمستان، در کشور در برههای از زمان، مازاد گندله و کنستانتره وجود دارد و بیشتر محصولات میانی صادر میشود و چارهای نیست؛ چون بسیاری از کشورهای خریدار محصولات میانی برای محصولات نهایی عوارض وارداتی وضع میکنند؛ بنابراین صادرات محصولات تولیدی مازاد بر نیاز چرخه زنجیره فولاد کشور، حائز اهمیت است.
توسعه صادرات کشور میتواند یکی از اولویتها باشد. در طرح جامع فولاد اشاره شده است که ایران باید در افق 1404 حداقل به 15 میلیون تن صادرات فولاد برسد، گرچه ممکن است حتی به این هدف دست پیدا نکنیم، اما در اصلاحیه و پایش های بعدی این طرح، اشاره به 20 میلیون تن صادرات نیز شده است. در واقعیت این اهداف با توجه به شرایط فعلی و امکانات و محدودیت بازارهای هدف یک مقدار دور از ذهن به نظر میآید.
بهرهوری در صنعت فولاد کشور
بهرهوری قیمت تمام شده یک محصول است. در کشور ما هزینه بالاسری تولید فولاد بالا است؛ نیروی انسانی زیاد و تکنولوژی قدیمی که باعث هدررفت انرژی و حتی هدررفت نیروی انسانی میشود.
در حال حاضر در تولید فولاد دو تکنولوژی جدید در ایران اجرا میشود که شروع استفاده از آنها به زمان برجام برمی گردد. در این تکنولوژی ها در پروسه تولید فولاد نهایی شامل ورق و یا میلگرد، تولید محصول میانی حذف شده و فولاد مذاب بهطور مستقیم در پروسه ریختهگری برای تولید ورق و میلگرد استفاده میشود و در این پروژهها، اِسلب و بیلت حذف شده اند که خود باعث صرفهجویی اقتصادی شده و هدر رفت انرژی را کاهش میدهد.
در پروسه تولید فولاد میانی، یکبار فولاد مذاب تولید میشود و بعد از اینکه مواد سرد شدند به کارخانههای نورد انتقال پیدا میکنند و مجدد با ایجاد حرارت، فولاد نرم شده و آن را برای نوردکاری استفاده میکنند. تمامی این مراحل باعث افزایش مصرف انرژی و هزینههای جابهجایی شده و در نهایت کاهش بهرهوری را به همراه دارند. بهره وری در صنعت فولاد کشور مثل خیلی از صنایع دیگر نسبت به استاندارد جهانی پایینتر است، اما نمیتوان این موضوع را بهعنوان یک ضدارزش حساب کرد، چون این نوع تولید در خیلی از کشورهای جهان و حتی در فولادسازهایی که در رتبههای جلوتر از کشور ما (ایران رتبه دهم در تولید فولاد جهان) هستند، وجود دارد.
فراموش نکنیم که کشور ما حدود 40 سال تحت تحریم بوده و تنها در بازه زمانی کوتاهی دچار تحریم نبوده ایم. این محدودیتها خودبهخود تأثیرگذار هستند و همین مقدار هم که توانستهایم رتبه دهم تولید فولاد جهان را حفظ کنیم، کار بسیار بزرگی انجام دادهایم و قابلتحسین است. قابل ذکر است اطلاعات تکمیلی در موضوع بهرهوری را میبایست مهندسین و صاحبنظران در رشته متالورژی با اشرافی که به پروسه تولید فولاد دارند، توضیح دهند.
نقد زنجیره ارزش فولاد در کشور
در نقد زنجیره ارزش فولاد در کشور و زیرساختهای مربوط به آن میتوان مواردی به شرح زیر بیان نمود:
– عدم توازن مبحثی است که بارها و بارها به آن تأکید شده و حتی شرکت فولاد تکنیک که مسئولیت تحریر طرح جامع فولاد کشور را برعهده دارد، به آن اشاره نموده است. با توجه به استانداردهای بینالمللی فولادسازان، عمدتاً جانمایی این نوع صنایع در اکثر کشورهای جهان نزدیک به دریا میباشد، اما در کشور ما حداقل در طول 30 سال گذشته نیازهای استانی مطرح بوده و نمایندگان محترم مجلس سعی کردند که این پروژهها را در استانهای موردنظر جانمایی کنند که بعدها مشخص شده با بحران کمبود آب روبهرو هستیم و پروژههای متعددی با هزینه های بالا برای انتقال آب از خلیجفارس و دریای عمان تعریف شده است.
– بحران دیگری که در کشور وجود دارد، محدودیتهای حملونقل است؛ شبکه ریلی و جادهای کشور، توسعه لازم را پیدا نکرده است، چون زیرساختهای لازم نیاز به سرمایهگذاری وسیعی داشته است. در واقع آن مقداری که برای شبکه ریلی در کشور مشکل وجود دارد در رابطه با واگن و لوکوموتیو نبوده و یا بسیار کمتر از شبکه ریلی است. تاکنون شرکتهای معدنی و فولادی برای خرید لوکوموتیو، واگن و کامیون سرمایهگذاریهایی کردهاند، ولی جادهسازی و ریل سازی کار این شرکتها نیست و باید توسط دولت و حاکمیت انجام شود.
– بنادر نیز بهعنوان زیرساخت با محدودیتهایی روبهرو هستند. اگر قرار باشد در آینده به صادرات 15 تا 20 میلیون تن فولاد برسیم، ظرف چند سال آینده نیاز است که بندرها ضمن افزایش تعداد اسکلهها، قابلیت پهلوگیری کشتیها با ظرفیت بالاتر را داشته باشند.
بسیاری از شرکتهای معدنی و فولادی نسبت به تأسیس نیروگاههای اختصاصی اقدام نموده و مجبور شدهاند که برق تولیدی را وارد شبکه کنند و حتی خودشان در پیک مصرف دچار کمبود برق شده اند. در مورد توسعه میدانهای گازی، شرکتهای بزرگ معدنی و فولادی پیگیر هستند که سرمایهگذاری انجام دهند، ولی زمانبر است و علاوه بر اینکه باعث ایجاد عدم توازن در زنجیره شده، موجب میشود در فصول مختلف با مازاد بعضی از محصولات که در فصول دیگر دچار کمبود هستند، روبهرو شویم.
درست است که ظرف 14 سال آینده، کشور دچار کمبود سنگآهن میشود و بایستی اکتشافات جدیدی اتفاق بیفتد و نیاز کشور است، اما من معتقدم بایستی درآمدی که در کل زنجیره فولاد کشور از صادرات محصولات بالادستی گرفته تا میانی و پاییندستی به دست میآید، به خود این زنجیره اختصاص پیدا کند و علیرغم اعتراض بعضی افراد مبنی بر اینکه باید محصولات بالادستی برای سالهای آینده ذخیره شود، بهتر است این محصولات هر چه سریعتر به پول نزدیک شوند؛ به عبارتی محصولات صادر و ارز وارد کشور شود.
همانگونه که با ورود ماشینهای الکتریکی نیاز به سوختهای فسیلی کاهش پیدا کرده و جایگاه نفت بهعنوان یک کالای استراتژیک سالبهسال ضعیفتر میشود، با وجود اینکه حداقل در نیمقرن آینده صنعت فولاد جزو صنایع اصلی خواهد بود ولی با پیشرفتی که در تکنولوژی حاصل میشود، در مورد سنگآهن نیز اتفاق مشابه خواهد افتاد.
بر اساس آماری که کشور چین در حدود سال 2015 منتشر کرد، قرار بود بهتدریج از سال 2020 مصرف سنگآهن در تولید فولاد در این کشور افزایش یابد و تا سال 2025 به پیک برسد و از سال 2025 کاهش پیدا کند؛ به این دلیل که با ورود تعداد بیشتر کارخانههای تولید فولاد بر مبنای کوره قوس الکتریکی یا Electric Arc Furnace بهجای کورههای بلند، استفاده از آهن اسفنجی و آهن قراضه بهعنوان خوراک افزایش پیدا میکند، اما شیوع کرونا بسیاری از معادلات را به هم زد و تمامی این موارد به تعویق افتاد. چهبسا اگر کرونا اتفاق نمیافتاد، در حال حاضر که نیمه اول 2024 هستیم، میبایست 25 درصد تولید فولاد چین با کوره قوس الکتریکی انجام شود، در صورتی که در حال حاضر چیزی حدود 17 یا 18 درصد است. قابلتوجه است که روند جایگزینی کورههای بلند به کورههای قوس الکتریکی با شدت دنبال میشود، اما کمی زمانبر است.
جمعبندی
در مجموع ظرف 50 سال آینده در صنعت فولاد کشور، سنگآهن بهعنوان مهمترین ماده اولیه برای تولید آهن و فولاد همچنان جزو مواد اولیه موردنیاز میباشد و باید به فکر اکتشافهای جدید باشیم. با توجه به ظرفیتهای کشورهای متعدد در منابع سنگآهن جهان، انجام پروژههای فراسرزمینی برای کشور مقداری دور از دسترس است و لذا باید بیش از هر چیز به منابع داخلی و فراوری منابع سنگآهن هماتیت و تبدیل آن به مگنتیت توجه کنیم.
فراموش نکنیم که در کنار این اقدام، باید توسعه صادرات کشور را در اولویت قرار دهیم و این موضوع مهمترین اصل است.
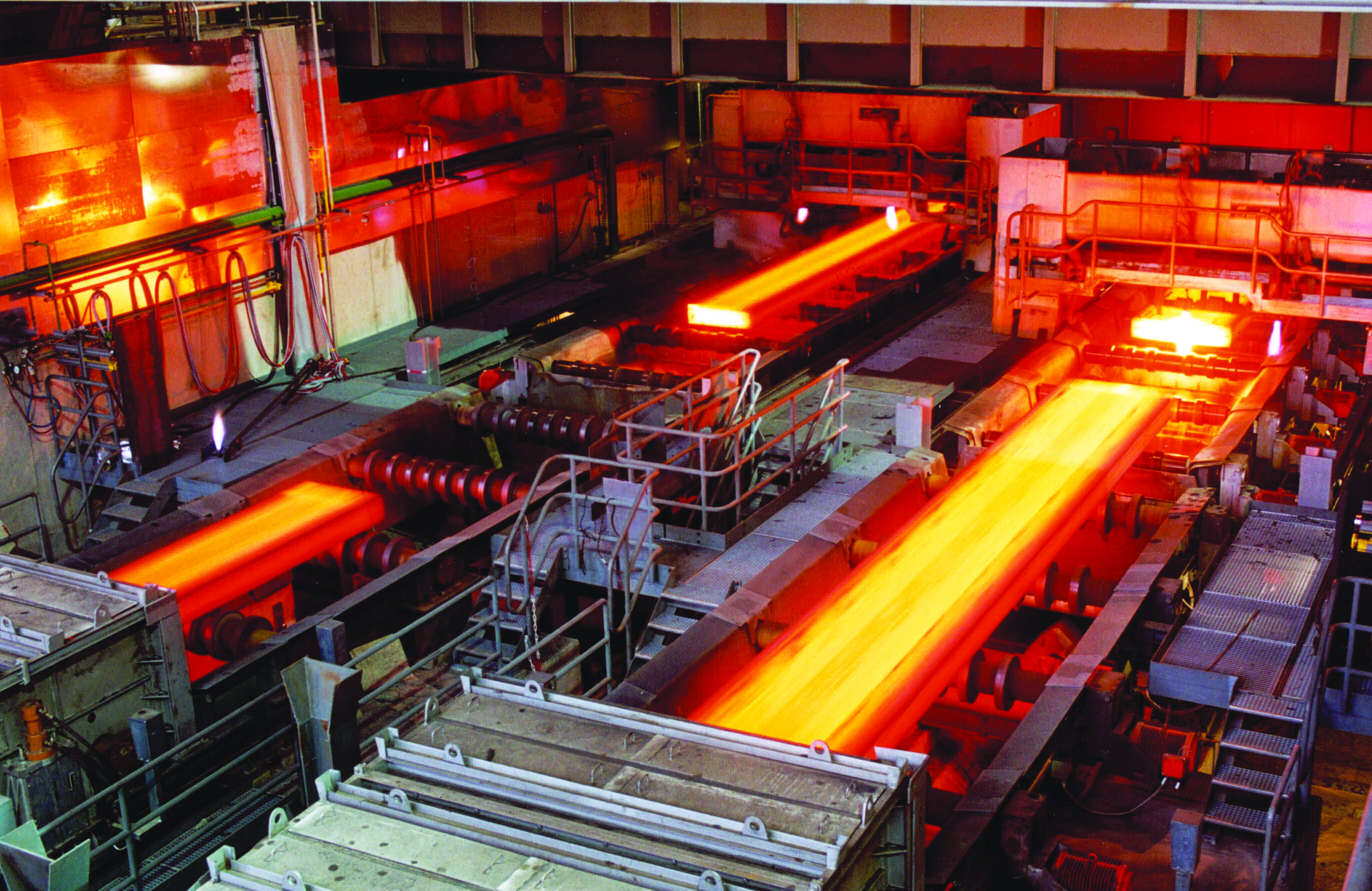